A Comprehensive Overview to the Process and Benefits of Plastic Extrusion
In the huge world of manufacturing, plastic extrusion emerges as a very effective and crucial process. Translating raw plastic into constant accounts, it provides to a huge selection of industries with its impressive flexibility.
Comprehending the Essentials of Plastic Extrusion
While it may show up complicated initially glance, the process of plastic extrusion is fundamentally straightforward - plastic extrusion. It is a high-volume production strategy in which raw plastic is melted and shaped into a continual profile. The procedure begins with the feeding of plastic material, in the form of granules, powders, or pellets, into a heated barrel. The plastic is then melted utilizing a mix of warm and shear, applied by a revolving screw. Once the molten plastic gets to completion of the barrel, it is required via a tiny opening called a die, forming it right into a preferred type. The shaped plastic is then cooled down, strengthened, and cut into desired lengths, finishing the process.
The Technical Refine of Plastic Extrusion Explained
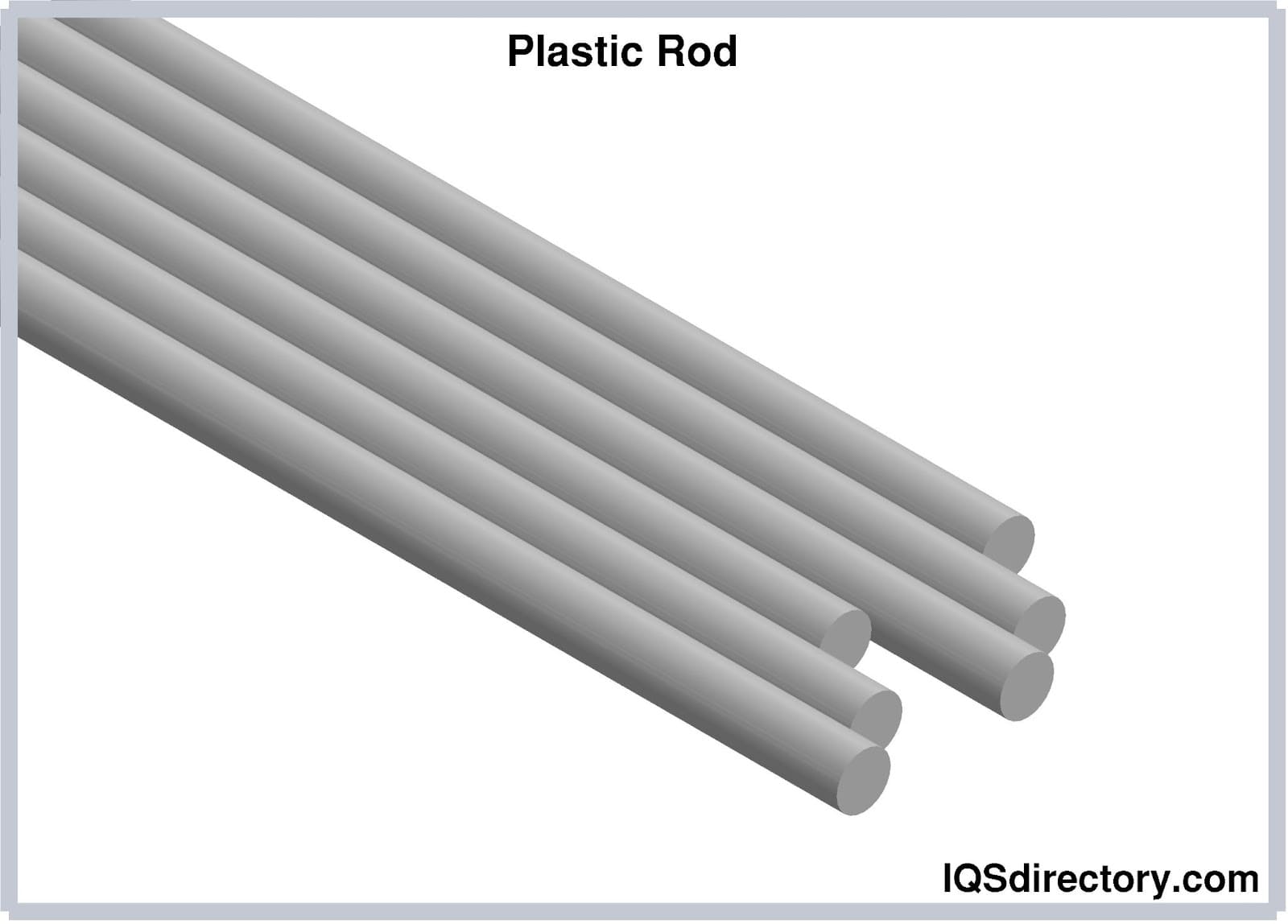
Kinds Of Plastic Suitable for Extrusion
The choice of the best sort of plastic is an essential facet of the extrusion procedure. Various plastics use one-of-a-kind buildings, making them much more suited to certain applications. Polyethylene, as an example, is commonly made use of because of its affordable and easy formability. It uses exceptional resistance to chemicals and moisture, making it suitable for items like tubes and containers. In a similar way, polypropylene is one more prominent choice as a result of its high melting factor and resistance to fatigue. For more robust applications, polystyrene and PVC (polyvinyl chloride) are commonly picked for their toughness and longevity. Although these are common alternatives, the choice eventually depends on the certain needs of the product being created. Understanding these plastic kinds can substantially improve the extrusion process.
Comparing Plastic Extrusion to Other Plastic Forming Approaches
Comprehending the sorts of plastic appropriate for extrusion leads the way for a more comprehensive discussion on exactly how plastic extrusion piles up against various other plastic creating methods. These consist of injection molding, blow molding, and thermoforming. Each technique has its one-of-a-kind usages and benefits. Shot molding, for instance, is exceptional for creating detailed parts, while strike molding is perfect for hollow things like containers. Thermoforming excels at forming large or superficial components. site Nonetheless, plastic extrusion is unmatched when it concerns creating continuous accounts, such as gaskets, seals, and pipes. It also enables a constant cross-section along the size of the product. Therefore, the selection of method mostly depends on the end-product demands and specifications.
Trick Benefits of Plastic Extrusion in Manufacturing
In the world of manufacturing, plastic extrusion offers lots of considerable benefits. One remarkable benefit is the cost-effectiveness of the procedure, which makes it a financially appealing manufacturing technique. Additionally, this strategy supplies superior item adaptability and boosted production speed, consequently raising total production effectiveness.
Cost-efficient Manufacturing Method
Plastic extrusion jumps to the center as an affordable manufacturing approach in production. In addition, plastic extrusion needs less power than standard manufacturing techniques, adding to reduced operational costs. Overall, the economic advantages make plastic extrusion an extremely appealing option in the manufacturing market.
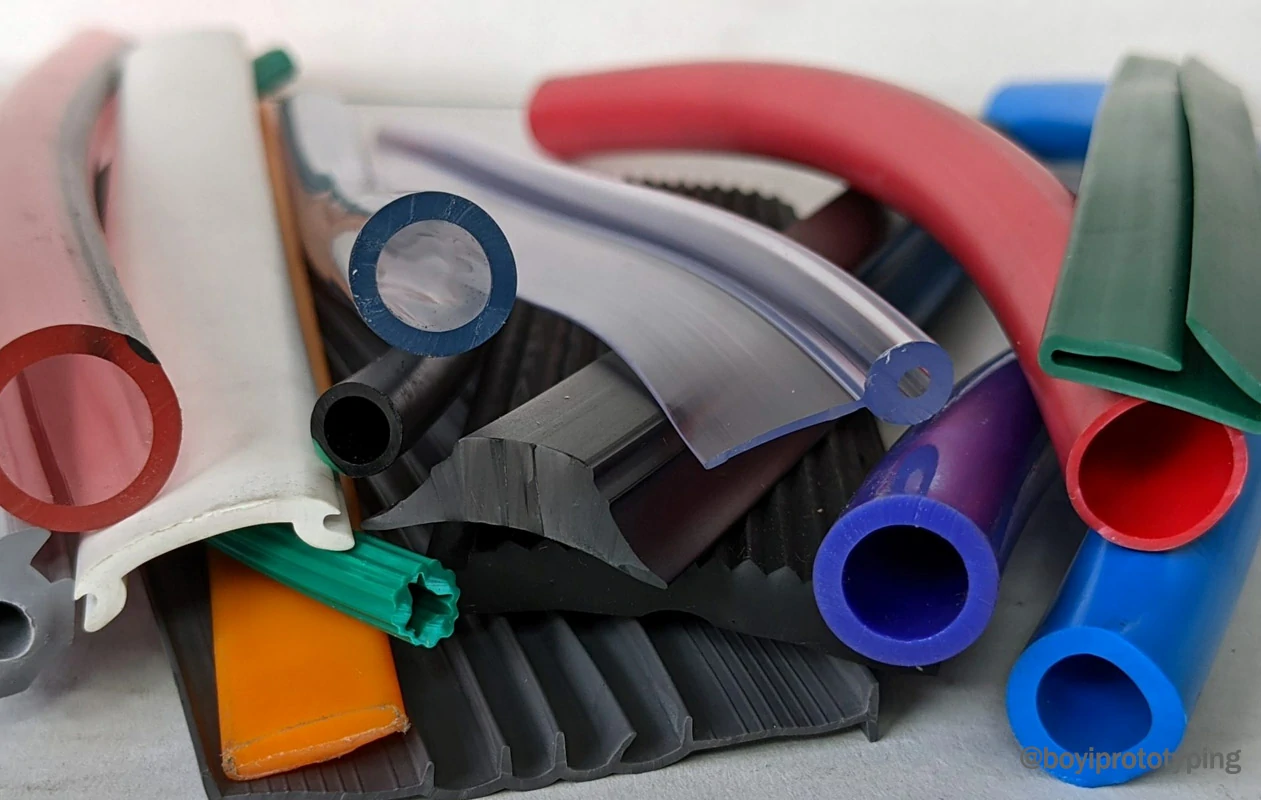
Superior Product Versatility
Past the cost-effectiveness of plastic extrusion, another considerable benefit in making hinge on its exceptional product versatility. This procedure permits the creation of a large selection of products with differing shapes, designs, and sizes, from basic plastic sheets to elaborate accounts. The adaptability is credited to the extrusion die, which can be personalized to produce the wanted item design. This my review here makes plastic extrusion an optimal solution for sectors that need personalized plastic components, such as auto, construction, and product packaging. The ability to generate diverse products is not only valuable in meeting details market needs however additionally in making it possible for suppliers to check out brand-new product with very little funding financial investment. In essence, plastic extrusion's item flexibility promotes technology while enhancing functional effectiveness.
Improved Production Rate
A significant advantage of plastic extrusion depends on its improved production rate. This production process permits for high-volume production in a relatively brief time span. It is capable of producing long, continual plastic accounts, which significantly decreases the production time. This high-speed manufacturing is particularly advantageous in industries where large amounts of plastic parts are required within limited due dates. Few other manufacturing processes can match the speed of plastic extrusion. In addition, the ability to maintain consistent high-speed manufacturing without compromising product quality sets plastic extrusion besides other methods. The boosted manufacturing rate, consequently, not only enables suppliers to satisfy high-demand orders but likewise adds to boosted efficiency and cost-effectiveness. This useful feature of plastic extrusion has actually made it a favored option in many markets.
Real-world Applications and Effects of Plastic Extrusion
In the world of manufacturing, the strategy of plastic extrusion holds profound relevance. This process is widely used in the manufacturing of a variety of products, such as plastic tubing, home window frameworks, and weather stripping. Consequently, it greatly influences sectors like building, product packaging, and automotive markets. In addition, its influence includes everyday things, from plastic bags to tooth brushes and disposable flatware. The financial benefit of plastic extrusion, discover here mostly its affordable and high-volume outcome, has reinvented production. The ecological effect of plastic waste remains an issue. For that reason, the sector is persistently aiming for innovations in recyclable and naturally degradable materials, suggesting a future where the benefits of plastic extrusion can be maintained without jeopardizing ecological sustainability.
Verdict
In final thought, plastic extrusion is a highly efficient and efficient technique of changing raw products right into varied products. It provides countless advantages over other plastic developing methods, including cost-effectiveness, high result, very little waste, and layout flexibility. Its influence is exceptionally felt in various sectors such as building and construction, auto, and durable goods, making it a pivotal procedure in today's manufacturing landscape.
Diving deeper into the technical procedure of plastic extrusion, it begins with the selection of the suitable plastic material. Once cooled down, the plastic is cut into the needed sizes or wound onto reels if the product is a plastic film or sheet - plastic extrusion. Comparing Plastic Extrusion to Other Plastic Forming Approaches
Comprehending the kinds of plastic suitable for extrusion paves the means for a broader discussion on exactly how plastic extrusion stacks up against various other plastic developing approaches. Couple of other production processes can match the speed of plastic extrusion.